Everyone loves ice cream, whether it’s the sweltering summer or the unplanned ice party over the year. With the best ice cream machines, VEVOR makes cold treats that joyfully fill your stomach. But sometimes, if your machine stops working, you need to look at some troubleshooting steps a VEVOR ice cream machine needs.
You might have several problems if your VEVOR ice cream machine needs to be repaired, such as overfilling or underfilling, damage to the powder cord, or a jammed paddle.
But don’t worry; read this article to understand the main issue and ice-cream machine troubleshooting process.
VEVOR Ice Cream Machine Common Problems & Troubleshooting Guide
Throughout this guide, you’ll discover the most common reasons why your ice cream maker isn’t working and how to fix them. By doing this, you’ll diagnose the issue quickly and get back to making frozen treats in no time.
1. My VEVOR Ice Cream Machine Won’t Run
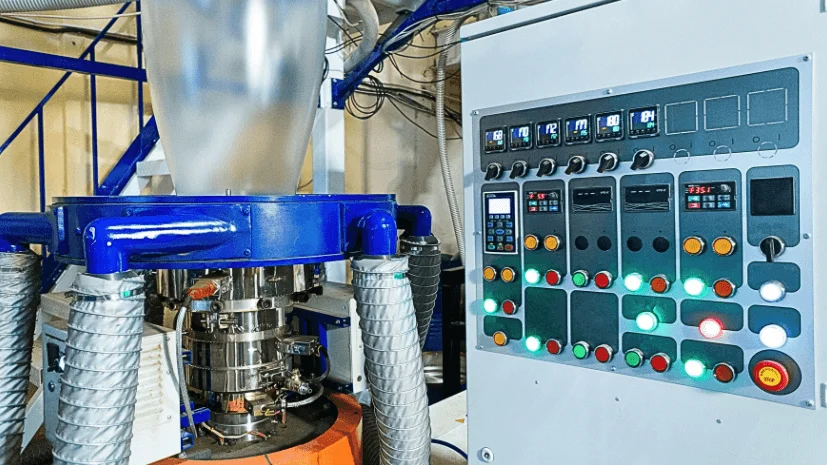
After pressing the auto button, if you see the ice cream machine freezer isn’t operating well and not freezing ice cream, then check out for the possible reasons below:
● Fuse is blown, or the circuit breaker is off: There’s a need to be on the circuit breaker, or blown a fuse should be replaced.
● Unplugged machine: Plug back the power cord if it’s unplugged from the socket.
● Cease beater motor on reset: To reset the freezer, reset the motor and contact any authorized technician for assistance if the issue is still there.
2. Why is My Ice Cream Machine Not Dispensing
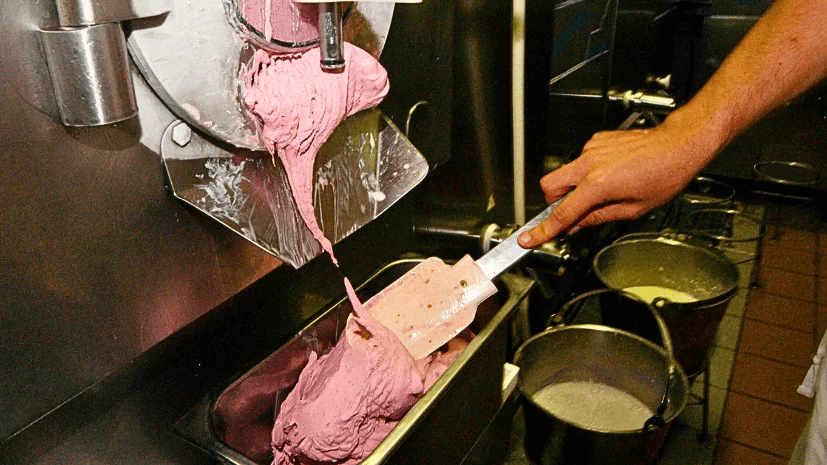
Check out your machine for potential problems if you’re having trouble with your machine.
● Frozen Mixture: If the mixture in the machine is not defrosted properly and frozen, it causes the machine to freeze or take longer to dispense the mixture. So, thaw and freeze the mixture correctly.
● Pump pressure or low overrun settings: If the pump pressure and overrun setting are too low, examine it and contact the technician to diagnose and repair your ice cream machine.
● Overloaded drive motor: If the drive motor overloads, the machine can reset. But if the same issue persists, then contact an authorized technician after trying the troubleshooting process of VEVOR ice cream.
● Low Refrigerant Charge: There might be an issue with the refrigerant charge, so it needs to be fixed by an authorized technician.
● Enormous air packets: In the barrel, oversized air packets can cause problems in dispensing. At that moment, you need to remove air from the barrel.
● Drive belt might be broken: Replace the broken and failed drive belt with a new one.
● Empty Hopper: Check and fill the hopper if there’s no mixture when the VEVOR ice cream machine is not freezing.
Recommended For Your Project
3. Machine Not Operating Properly
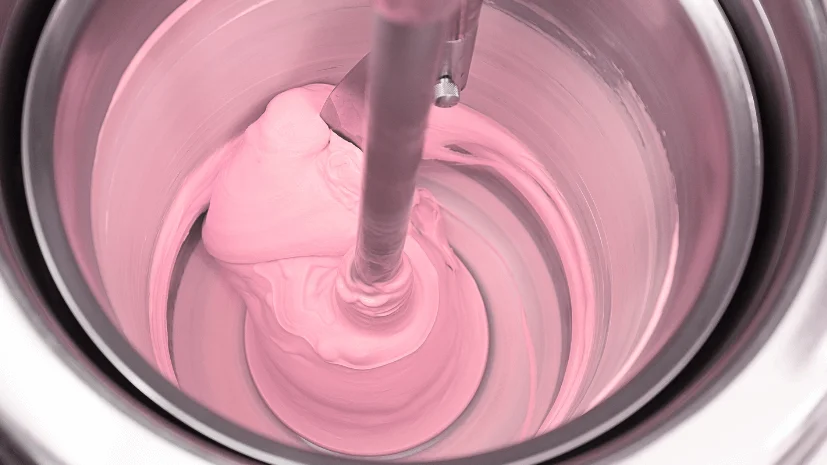
Check out the reasons for troubleshooting your VEVOR ice cream machine.
● No Power: Examine if the power cord is unplugged and the machine is turned off. If that’s okay, look for a blown a fuse and tripped circuit.
● Voltage is low: Low voltage supplied to the unit or the call the technician to diagnose the issue and correct it.
● Auger not turning: Wait 15 minutes to turn on the auger and switch the unit off.
● A faulty drive motor: The machine compressor prevents it from operating if the drive motor is overloaded. To reset the drive, press the “Drive Reset” lever. Contact an authorized technician if the issue is still there.
● Incorrectly installed door: If the front door is installed incorrectly or loose, install it securely.
4. Machine Leakage Problem
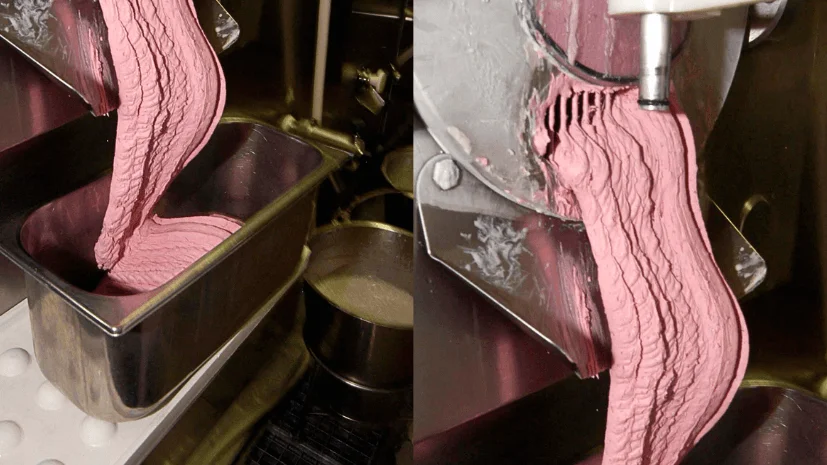
Machine leakage can be due to different reasons and requires ice-cream machine troubleshooting.
● Unlubricate Spigot and Auger Seal Parts: Lubricate these parts according to the given instructions to lubricate these parts accordingly.
● Improper O-rings installations: Replace the O-rings when they’re worn or chipped. Correct the placement and remove the spigot.
● Improper seal: Examine missing and improper seals. Please read the manual guide to learn how to align it.
● Broken Shaft: Observe notable wear and scratches. A technician can replace the shaft.
5. Squeaking Drive Belts
Look out for the possible troubleshooting process for a VEVOR ice-cream machine if you find a squeaking driving belt.
● Improper drive belt tension: Using manual instructions, adjust the drive belt.
● Damaged Belt: Replace the damaged belt with a new one.
6. Too Thin or Soft Ice-cream
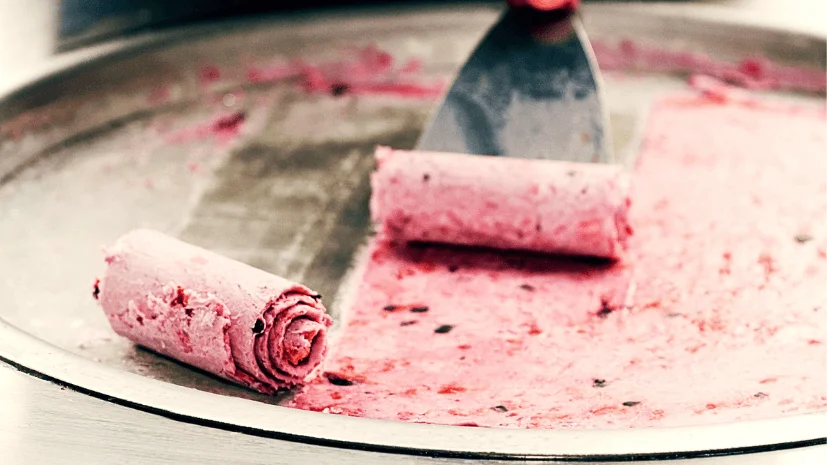
When you observe the extraordinary soft ice cream coming out, look for further reasons for troubleshooting the soft serve ice cream machine.
● Extremely High Outside Temperature: Your ice cream can be softened if the unit faces direct sunlight. The unit entering air should be below 100°F. Considering changing the unit place to a cooler spot.
● Consistency Setting Can be Low: To firmer the product, adjust the consistency settings on your ice cream machine.
● Clean the dirty condenser: The dirt in the condenser can be the reason for the machine overheating. Make a habit of cleaning the condenser once every three months.
VEVOR Ice Cream Machine Preventive Maintenance Tips
If you want to get the best out of your VEVOR ice cream machine, regular maintenance and cleaning are the essential steps you can take. Before jumping into further maintenance methods, we recommend you look at the cleaning steps.
1. Cleaning of the tank and freezing cylinders
To improve the machine part life and health, improve the service life. It’ll be helpful to clean the freezing cylinder and disinfect it whenever it’s used.
To do this, follow the steps:
● To discharge all the sludge in the tank, press the cleaning button, and after pressing it twice, the machine will stop.
● Use disinfectant and hot water appropriately, almost 70% of the tank amount.
● Before draining the solution, stir it for about 5 minutes after pressing the cleaning button.
● Wash it with water twice or thricely, then stop.
● To clean the chute discharge port, use a cleaning brush.
● With a clean cloth and a clean brush, clean the liquid level sensor with a cloth. Material shortage alarm will only work if the cleaning is completed. After removing the mixing blade, the rotating shaft is removed with a clean cloth. Ensure the groove inside the rotating shaft is cleaned with a cleaning brush. Wipe the tank clean.
2. Cleaning and Removing Parts of Ice Cream Machine
● Pull out the four nuts and remove the discharge valve. Disassemble and clean the parts of the discharge valve, starting with the handle, handle fixing pin, and sealing rings in sequence. In the freezing cylinder, remove the agitator. Follow the opposite steps to reinstall the cleaned parts.
● Disassemble and clean the parts of the discharge valve, starting with the handle, handle fixing pin, and sealing rings in sequence. In the freezing cylinder, remove the agitator. Reinstall the cleaned parts by following the opposite steps.
3. Body Maintenance of Ice-cream Machine
● Before cleaning, the switch for the body control must be off. Clean and dry it with a soft cloth. Use a warm towel sprayed with dish soap to remove the stain if the soil is dirty. Furthermore, the base and lower parts of the machine can be prone to contamination. So, clean it carefully.
● The drain-pipe goes into the machine’s water tank from the inside. If you find the raw materials in the drain pipe, it can be due to a defective motor shaft in the freezing cylinder deep part. For this, you’ll need to talk to maintenance.
● To not damage the outer surface of the machine, it’s advised not to use hot water, polishing and gasoline. Examine the power cord twice, and if found damaged, then replace it.
4. Condenser Cleaning and Maintenance
● Cover the condenser if you’re working, as it’ll affect due to the heat dissipation. Clean it twice and ask for professional help in this matter. Before cleaning, unplug the power cord to avoid damaging the condenser fins.
FAQs about VEVOR Ice Cream Machine Troubleshooting
1. What precautions should be taken during installation?
Uninsulated wiring and terminals should be protected and taped to avoid fires, electrical shocks, and injuries. It is never a good idea to push any object through a slot in a product.
2. How should the ice cream machine be placed?
Ensure the machine is in a cool place away from heat sources and walls that might block air circulation.
3. How do you clean a VEVOR soft-serve ice cream machine?
The first step in cleaning your VEVOR soft-serve ice cream machine is to flush out all the product mix. Clean with warm water and a cleaning solution. Let it run for approximately five minutes, then empty it. Disassemble the machine, dip a brush in the same cleaning solution, and brush each component.
4. Why is my ice cream maker overheating?
Overheating equipment is caused by jammed paddles, stretched motors, and damaged power cords. Change your operating and cleaning habits if you think your equipment is overheating.
5. What is the warranty period for the VEVOR Ice Cream Maker?
VEVOR Ice Cream Machines have various warranty periods based on the model and manufacturer. Warranty periods typically range from one to three years.
Bottom Line
Your machine needs maintenance and cleaning to last a long time. Do the VEVOR ice cream machine troubleshooting by following the different steps. Don’t hesitate to contact a commercial ice cream machine repair technician if your ice cream machine doesn’t start working after troubleshooting.