Air compressors are very important tools that are used in many different industries, from automotive repair to construction and much more. This is thanks to their ability to power many different pneumatic tools and equipment.
They’re very efficient, versatile, and can perform many different jobs. Today, we’re going to write about the inner workings of air compressors and talk about how they operate and what types are available.
Moreover, we’ll also talk about the different uses of air compressors across different industries and give you some answers to the most frequently asked questions about how air compressors work.
Air compressors like the VEVOR 80 Gallon Air Compressor are perfect for powering a variety of pneumatic equipment, whether at home or on the job site. So, how does an air compressor work?
Table of contents
What Is an Air Compressor?
So, first things first, an air compressor is a special type of device that takes power, usually from a gas or electric engine, and turns it into potential energy that is stored in the form of compressed air.
This compressed or pressurized air can then be used to power a variety of machines and tools, making air compressors extremely important for a wide variety of industries.
Air compressors are able to continuously supply compressed air or store it within a tank, depending on the application in question. This process usually starts withdrawing in air, compressing it, and then putting it in the tank until it’s needed.
This stored energy which is in the form of pressurized air can then be released in bursts, which provides consistent power for tools that need pressurized air, whether they be spray guns, impact wrenches, or nail guns. As you’ll see further below, air compressors come in many different types.
What Is an Air Compressor Used For?
Air compressors can be used for many different purposes, which is exactly what makes me so versatile and useful in many different industries. For instance, air compressors are often used in the construction sector, where they are used to power tools such as concrete compactors, drills, and jackhammers, as well as anything else that requires a great deal of power in bursts.
Furthermore, air compressors are also used in automotive repair shops, as they are very useful in this setting as well. They can be used for powering a wide variety of pneumatic tools, such as pneumatic air wrenches, as well as for painting and tire inflation. Furthermore, air compressors are also used in the manufacturing industry, where they help with assembly lines and air-powered machinery.
If you happen to be a homeowner or DIY enthusiast, you might also use an air compressor to power paint sprayers, sand surfaces, or inflate tires. In any industry that requires precise air control, such as in the medical and dental industries, air compressors come in very handy as well.
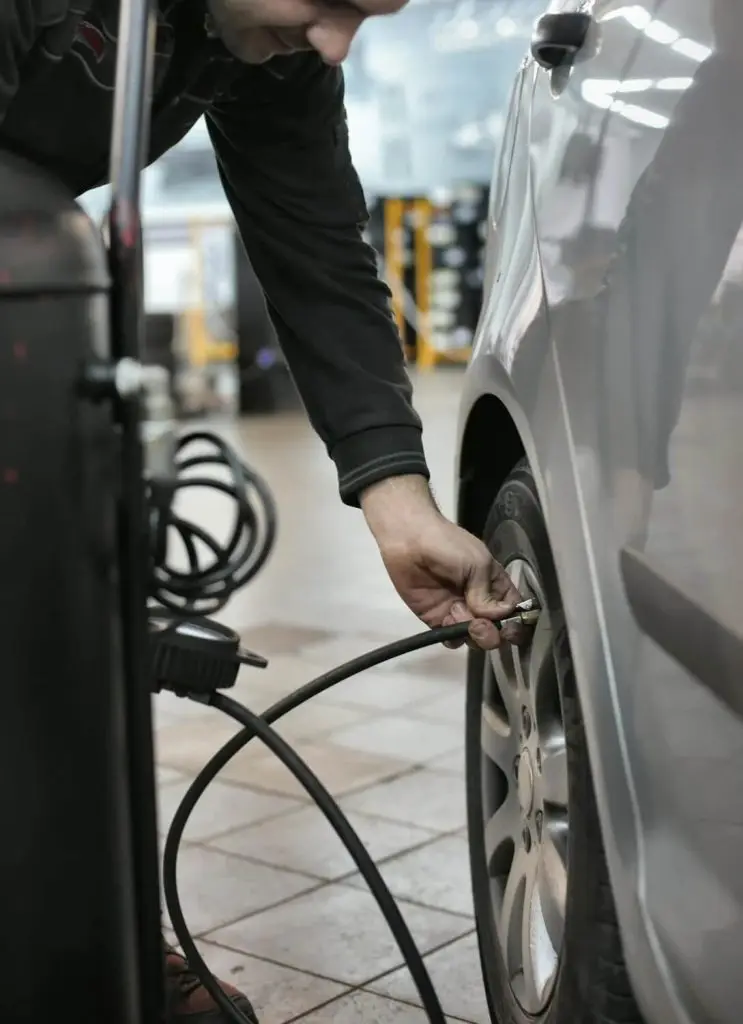
How Do Air Compressors Work?
Air compressors are in theory very simple tools, as they revolve around the principle of drawing in air, compressing it, and thereby increasing its pressure.
Intaking Air
This process all starts with the air intake, where an air compressor starts pulling atmospheric air in through the intake valve. Many air compressors feature air filters in the intake valve system to stop debris from getting into the machine.
Compressing Air
Next, once the air is inside the machine, a piston or a rotor is used to compress it. Exactly how the air is compressed depends on the compressor style, which is something we’ll take a closer look at below.
Direct Use or Storage
The air that is compressed is then supplied directly for immediate use with a variety of tools, such as spray guns or nail guns, or the compressed air can also be stored in a tank for future use.
Keep in mind that there are tankless air compressors which can always supply a steady supply of air, whereas compressors that come with storage tanks can supply air steadily while also being able to offer bursts of high-pressure air whenever required.
Control of Pressure
The vast majority of air compressors in existence today also come with pressure regulators or pressure gauges. These are used to monitor and adjust the pressure being put out according to the requirements of the task at hand. Once the air pressure in the tank reaches a specific level, the compressor then shuts off automatically to conserve energy.
Releasing Air
Once you activate the attached tool, such as a nail gun, the air from the tank or compressor is released, thereby delivering you with all of the power you need to operate the tool.
Auto Shut-Off Features
To finish things off, many air compressors feature automatic shut-off mechanisms to prevent overheating, along with oil-free components to reduce friction and maintain ideal temperatures, with the VEVOR 80 Gallon Air Compressor being a prime example.
Recommended For Your Project
Different Types of Air Compressors and How They Work
What’s also important for you to know is that there are different types of air compressors, and they all function in slightly different ways.
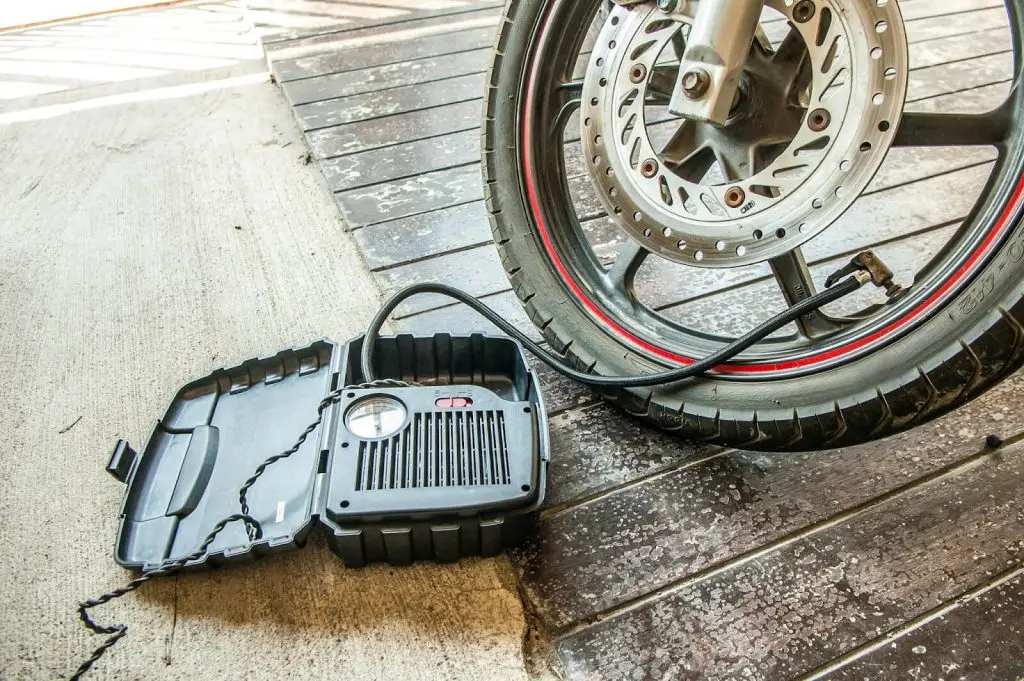
Reciprocating or Piston Compressors
Reciprocating compressors are some of the most popular options due to their reliability and straightforward design. They have a crankshaft that drives pistons with cylinders to compress the air.
There are both single-acting and double-acting models, where either only a single or both sides of the piston are used, respectively.
Double-acting models have much higher power outputs. These compressors are great for heavy-duty applications, particularly in industrial and automotive repair industries.
Rotary Screw Compressors
We then have rotary screw compressors, which use two screws or helical rotors that rotate in order to compress the air in between them.
The fact that they feature continuous operation makes them a great choice for large-scale applications that require a steady supply of pressurized air, such as on construction sites and in factories.
These compressors are known for their durability and efficiency, as they don’t generate a whole lot of heat. Rotary screw compressors often feature an oil injection mechanism to help lubricate the screws.
Centrifugal Compressors
Next on the list we have centrifugal compressors, which are also known as dynamic compressors. These use very fast-moving impellers to accelerate air and compress it. Once the air has passed through the impellers, it has gained a lot of kinetic energy, and this is converted into pressure.
This is ideal for producing very high volumes of pressurized air at a steady rate, making them ideal for applications that demand a lot of power, such as in steel manufacturing facilities or chemical processing plants.
Oil-Free Compressors
We then have oil-free compressors, which do not use any kind of oil for lubrication but instead use pre-lubricated materials or feature special coatings to reduce wear and friction.
This makes oil-free compressors great for environments that require clean air, such as medical facilities, food processing plants, and laboratories.
These air compressors avoid oil contamination, therefore offering much cleaner air, although they generally have a lower lifespan due to the lack of lubrication.
Portable Compressors
Finally, we have portable air compressors, which are small, lightweight, and compact. They’re ideal for job sites that require on-site power, such as for inflating tires, powering airbrushes, or powering nail guns. They generally have lower outputs than stationary compressors, but are also more portable.
FAQs
Let’s quickly answer some of your most frequently asked questions about air compressors.
How often should an air compressor be serviced?
If you are using the air compressor on a regular basis, such As for daily use, then checking oil levels and filters should be done every two or three weeks at the most. If you use the air compressor moderately, about once per month should do fine.
Can air compressors be run continuously?
This depends on the type of air compressor in question. For instance, reciprocating compressors are best suited for intermittent use and short bursts of power, whereas rotary screw compressors are best for continuous operation and for steady flows of air.
What makes single-stage and two-stage compressors different?
Single-stage air compressors only compress the air once, therefore making them best for lighter tasks. On the other hand, two-stage air compressors compress the air twice, therefore providing a lot more pressure, and thus being ideal for heavier-duty applications.
Are air compressors loud?
Exactly how loud an air compressor is really depends on the model. However, if we’re looking at something like the VEVOR 80 Gallon Air Compressor, this is known for being extremely quiet. It produces only 86 decibels of noise, therefore making it one of the quieter models on the market.
How an Air Compressor Works: Final Thoughts
The bottom line is that air compressors work by drawing in air and compressing it using a variety of mechanisms, which depends on the exact type of air compressor in question. However, the bottom line here is that between all of the different air compressors out there, you can easily find a model that works for your application. Remember, models like the VEVOR 80 Gallon Air Compressor are suitable for a wide variety of tasks thanks to their versatile designs.