Whether you’re working in a home garage or an industrial workshop, an air compressor is an essential tool to have. They enable the use of pneumatic tools, spray painting, and many other equipment. Air compressors play such a crucial function that their importance in a workshop is often compared to that of electricity in terms of how our modern world is powered.
The question of how long an air compressor will last is critical for anyone thinking about buying one or currently using one. Your equipment needs to be durable so it can withstand the test of time. Air compressors, if handled with the right care and attention, can last for many years and serve you well.
If you’re in the market for an air compressor, keep in mind that its durability is directly proportional to its quality. As such, we will advise that you invest in the VEVOR Air Compressor. The VEVOR Air Compressor excels amongst its competitors due to its exceptional features that guarantee super performance and longevity. It runs at 86 dB, guaranteeing ultra-quiet operation. This lessens the impact of operation, and its super-big capacity of 80 gallons gives a longer duration of consistent air supply.
Table of contents
How Long Do Air Compressors Last?
The type of compressor, the frequency of usage, and the adherence to maintenance schedules are some of the variables that affect how long an air compressor lasts. If you take good care of your air compressor, it should last anywhere from five to twenty years.
Lifespan of Different Types of Compressors
A wide variety of air compressors are available, and they all have different expected lifetimes. The following are the estimated lifespans of some of them:
- Reciprocating air compressors: Common in smaller workshops and garages, reciprocating air compressors may run for nearly ten years with the proper maintenance.
- Rotating screw compressors: Famously known for their durability, rotating screw compressors can often last for ten years or more, or an equivalent of 100,000 hours.
- Centrifugal air compressors: These impressive machines can handle high-pressure and high-volume tasks for up to twenty years, or 150,000 hours.
Regarding VEVOR Air Compressors, these machines boast state-of-the-art technology and a robust design to ensure they last for many years. Not only do they supply the required compressed air, but they also eliminate the wear, pollution, and maintenance issues caused by oil lubrication.
Enhancing Durability Through Best Practices
If you want your air compressor to endure as long as possible, consider following these best maintenance practices and tips as recommended by experts:
- Schedule professional inspections on a regular basis to catch issues in their early stages.
- Keep moving parts well-lubricated to reduce heat and friction.
- Keep the compressor clean on a regular basis to prevent the accumulation of dirt and dust.
- Regular filter changes are necessary to keep the airflow clean.
- Inspect for and seal leaks on a regular basis to keep your system running efficiently.
What Determines the Lifespan of an Air Compressor?
The number of years that an air compressor can last is dependent on a number of elements, each of which is important in its own right. Quality, utilization, and care put into these potent tools are more important than just numerical values on a page. We have discussed the major factors that determine the lifespan of these machines below.
Quality of Materials and Manufacturing
A high-quality air compressor starts with good materials and craftsmanship. Air compressors made with high-quality materials and careful engineering will last much longer. For example, industrial-grade compressors can withstand harsh environments and heavy use for a long time. Conversely, compressors constructed with inferior materials may experience premature wear and tear, necessitating repairs or replacements more frequently.
Usage Frequency and Intensity
The durability of an air compressor, just like any well-oiled equipment, is dependent on the frequency and intensity of its use. In essence, its quality and need for maintenance will increase in relation to the amount of times you use it, and the volume of work it does.
Operating compressors under high pressures for long durations increases the stress they undergo, which in turn reduces their lifespan. To have a long-lasting relationship with your compressor, you need to strike a balance between performance and endurance, which requires mindfulness and moderation.
Regular Maintenance
Keeping up with routine maintenance is the best way to ensure that your air compressor lasts a long time. Being proactive instead of reactive is key. Maintaining it clean, well-oiled, and checking it often can do wonders. In addition to avoiding malfunctions, regular maintenance will guarantee better productivity and security.
Extending the Life of Your Air Compressor
Like tending to a precious relationship, keeping your air compressor in good repair will increase its lifespan. Dedication, learning about its requirements, and thoughtfully meeting those needs are key. Here we’ll explore maintenance tips, potential problems, and the logic for timely upgrades.
Routine Maintenance Tips
A thorough maintenance schedule is essential for the extended life of an air compressor. To ensure the efficient operation of your compressor, here are some maintenance tips to follow:
- Tank draining: Draining the water vapor that condenses in the tank can stop rust and corrosion.
- Tighten fasteners: Inspect for loose bolts and screws caused by vibration on a regular basis and tighten them if necessary.
- Hose inspection: Inspect hoses for damage or wear and replace them as necessary to keep pressure and prevent leaks.
- Keep the intake vents clean: Make sure your compressor can breathe easily by removing any obstructions.
- Change filters regularly: To keep pollutants out of the system, change the filters regularly. Clean air is essential to the performance of your air compressor.
- Check the oil levels: Always keep an eye on the oil level in your oil-lubricated compressor and replace it as the manufacturer instructs.
- Prevent the compressor from overheating by keeping the heat exchangers clean.
- To make sure the belts are working efficiently, check them for wear and strain.
- Verify the proper operation of safety shutdown systems by testing them on a regular basis.
Avoiding Common Pitfalls
Minor concerns now can cause major headaches later on. The following are some common pitfalls that you should do your best to avoid:
- Overheating: Do not operate in a hot, poorly ventilated area. Doing so can cause overheating.
- Leaks: Check for air leaks often. Air leaks reduce efficiency and increase operational expenses.
- Operation error: Read and follow the manufacturer’s instructions regarding the operations of your compressor and follow them to the letter.
Upgrading and Replacing Components
Compressor parts wear out with age. Your machine can be revitalized by upgrading and replacing parts such as filters, separators, and the motor. By upgrading and replacing worn out components, your air compressor will be able to keep up with your demands even as technology evolves. This is because regular upgrades ensure machine efficiency is maintained, which boosts performance.
The VEVOR Advantage: Built to Last
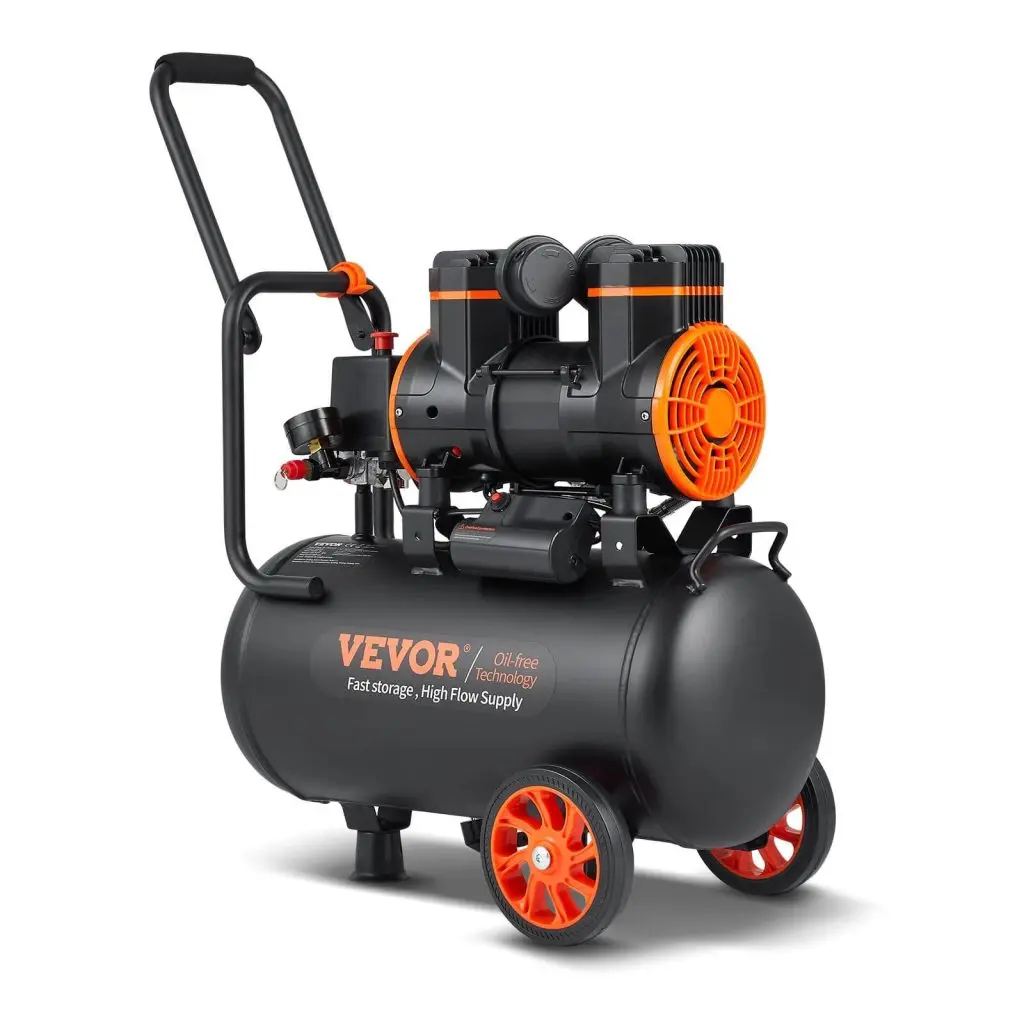
The ideal air compressor is one that not only gets the job done, but also does it efficiently and for a long period. As mentioned, we recommend the VEVOR Air Compressors in this regard. VEVOR Air Compressors are epitomes of pneumatic tool durability, and peerless performance. We explore these compressors below.
Superior Quality and Design
VEVOR never compromise on quality, and this is evident in our compressors. For context, our 80-gallon air compressor exemplifies their commitment to quality. The machine is built to withstand any task, and its 4mm high-strength steel plate ensures durability. You don’t have to worry about gas leaks or other safety concerns due to the excellent sealing performance assured by the painstaking welding and thermal machining procedures.
Optimized for Performance and Durability
In addition to being durable, VEVOR Air Compressors are also quite smart. Our 80-gallon model produces an astounding 15.5 SCFM at 90 PSI with its dual-stage compression technology and 6.5 HP oil-free engine. Because of this, instant inflation (within 6 minutes) is possible without compromising performance.
Aside from power, it’s also about sustainable operations. You can get work done without being interrupted by the compressor’s low noise level of 86 dB. This machine is ideal for both regular use and demanding jobs since it has an overheating protection feature that ensures it will remain cool under strain.
Troubleshooting Common Issues
At some point, every owner of an air compressor may encounter some difficulties. But don’t worry; with a little know-how, you can troubleshoot common issues and keep your compressor running like a champ. Here are some likely issues you’d encounter and the steps required to troubleshoot them.
Pressure Build-Up Problems
Compressor issues related to pressure buildup can be the cause of inefficient puffing from your device. Approach them using the following tips:
- Lubrication is important. If your compressor isn’t well-oiled, it could experience pressure problems. Thus, you should ensure to stick to proper lubrication.
- Make sure there are no air leaks; even a tiny one might cause substantial damage. Be sure to check for and repair any leaks in your system.
- You should check the pressure switch to see if your compressor is running continuously.
- Replace worn or damaged valves to keep your system running smoothly. Check them and, if needed, replace them.
- Check the rings on the pistons. When piston rings are damaged, it might cause pressure issues. Inspect them and, if necessary, replace any worn ones.
Maintenance Checklist
Maintaining a compressor requires routine inspections to ensure optimal performance. A checklist to assist you is provided here:
- Drain the tank of any excess moisture every day to keep it rust-free. Listen for and fix any leaks or strange noises.
- Air intake filters should be cleaned or replaced weekly, and all hoses and connections should be inspected for signs of wear or leakage.
- At least once a month, make sure all fasteners are snug and tight, and check the safety features.
- Check for and replace worn gaskets, belts, and other parts that could impact performance and efficiency once a year.
Conclusion
Air compressors are useful in a wide variety of settings for industrialists, DIYers, and several other craftsmen. As mentioned, choosing the right machine from a trusted manufacturer, and committing to daily maintenance can go a long way in helping you keep the compressor functioning at peak efficiency for as long as possible.
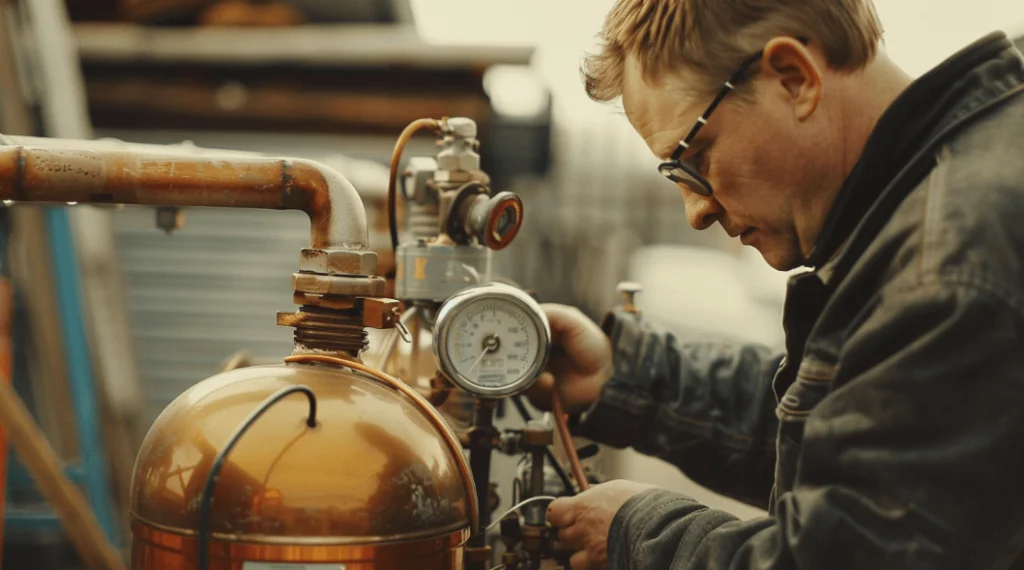
For optimal performance, investing in Air Compressors from VEVOR is a smart choice. Our model air compressors are made to handle tough work and built to last long. The features of our compressors are designed to help you get the job done right in record time. Consider visiting the VEVOR website to make an order today.
Ultimately, remember that the keys to increasing the lifespan of your compressor lies in being meticulous about its care and engaging in regular maintenance. Your air compressor will serve you for many years and aid you in executing several successful projects if you maintain and care for it properly.