Embarking on a metal fabrication project requires the right tools, and when precision and efficiency are paramount, a plasma cutter takes center stage. This cutting-edge technology employs a high-velocity jet of ionized gas to slice through metal with unparalleled accuracy. But just how thick can a plasma cutter cut? In this blog post, we set out to examine the cutting prowess of plasma cutters and explore the factors at play. In addition, we’ll recommend our handpicked collection of the best plasma cutters to empower your metalwork project. Join us as we unveil the secrets behind this versatile tool’s cutting prowess.
Table of contents
How Thick Can You Cut with a Plasma Cutter?
When we talk about how thick can a plasma cutter cut through, it is important to note that plasma cutters are a broad category with differing cutting depths. Basically, there are two types of plasma cutters: handheld plasma torches and automated plasma cutting machines.
So how thick of steel can a plasma cutter cut? Generally speaking, handheld plasma torches can cut steel plates of up to 38 mm in thickness. Stronger automated machines, on the other hand, have a much higher cutting ability, with some able to slice apart metal places of up to 150 mm in thickness.
However, note that these are only general figures, and the exact extent of how thick of metal can a plasma cutter cut varies among both handheld plasma torches and automated plasma cutting machines. Moreover, not only the cutter itself but also the workpiece plays a role in determining the maximum cutting thickness. In the following part, we provide a more in-depth account of the factors impacting the max cutting thickness.
Factors Influencing the Plasma Cutter Max Thickness
How thick can plasma cutters cut hinges upon a delicate interplay of factors. Among these factors affecting plasma cutter thickness, please take note of the following significant ones.
Power Source
The heart of a plasma cutter lies in its power source. Higher-amperage machines wield more cutting force, allowing them to effortlessly slice through thicker materials. Let’s take 50 amp and 100 amp plasma cutters as examples. How thick can a 50 amp plasma cutter cut? Typically, a 50 amp plasma cutter can cut a thickness of 15-20 mm. A 100 amp plasma cutter, on the other hand, has a maximum cutting thickness of roughly 40 mm.
Material Type
The type of material being cut influences the maximum thickness the plasma cutter can handle. Different materials have varying conductivity and thermal conductivity, affecting the efficiency of the cutting process. Generally, conductive materials like steel and aluminum are more amenable to the process. On the other hand, poorly conductive or non-conductive materials like wood, plastics, tungsten, and lead, are hard or impossible to cut using plasma cutters.
Type and Condition of Consumables
The consumables, including the nozzle and electrode, play a significant role in maintaining the cutting performance. Worn or damaged consumables can reduce the efficiency of the cutter and limit its ability to cut through thicker materials. Optimal nozzle selection ensures a focused and controlled arc, increasing the cutter’s ability to penetrate thicker materials.
Plasma Gas Selection
The type of gas used in the plasma-cutting process plays a role in determining the maximum thickness. Different gases, such as air, oxygen, or nitrogen, have varying levels of conductivity and affect the cutting speed and capability. Selecting the right gas for the material being cut enhances efficiency and influences the maximum thickness achievable.
Machine Design and Technology
The design and technological features of the plasma cutter itself, including its overall build quality, precision, and advanced features, can impact its ability to cut through thicker materials.
Operator Skill and Technique
The skill and technique of the operator play a vital role. An experienced operator can optimize the cutter settings, choose appropriate consumables, and control the cutting speed to achieve better results on a variety of material thicknesses.
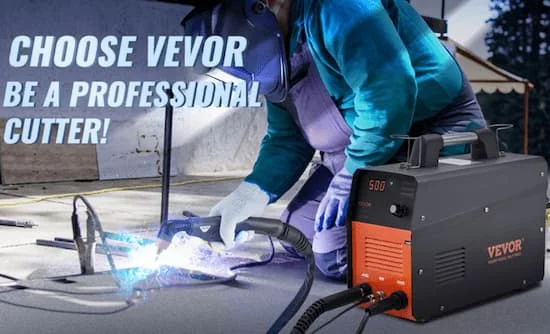
How Does Plasma Cutting Work?
In this part, let’s recap how plasma cutting works its magic on metal workpieces to get a fuller understanding of plasma cutters.
In a nutshell, plasma cutting uses plasma jets to melt metals. These jets, composed of ionized gas with a temperature of over 20,000°C, slice through metal pieces with intensity and precision.
As the cutting begins, a plasma arc is created between the torch and the workpiece by passing electric currents through a gas, typically compressed air or an inert gas. Since plasma is conductive, a circuit is formed between the torch and the workpiece, with the torch serving as the cathode and the workpiece as the anode. It is this plasma arc that does the cutting. As cutting continues, the gas nozzle of the torch discharges a stream of plasma, sustaining the cutting process.
The intensity of the plasma is directly tied to the cutter’s ability to cut. Typically speaking, the higher amperage the cutter has, the stronger the plasma arc will be, and hence the deeper the cutter can cut.
As a circuit must be formed in plasma cutting, plasma cutters can’t handle non-conductive materials like wood. However, compared to many other cutting technologies, it excels in both speed and precision when cutting lots of conductive materials, including mild steel, stainless steel, aluminum, and so on. This sufficiently explains why plasma cutting is extensively used across a variety of industries.
Best Plasma Cutters with Max Severance Cut
Now let’s learn about some exceptional plasma cutters with great performance. We’ll explore their cutting capabilities, and introduce some of their features that can facilitate the metalworking process.
VEVOR Pilot Arc Plasma Cutter
As a leading pioneer in plasma cutting technology, the VEVOR Pilot Arc Plasma Cutter transforms your metalwork project with its compelling merits. Delivering a current of 50 amp, it penetrates metals like aluminum, mild steel, stainless steel, copper, and other metals with power and precision, leaving smooth and aesthetic cuts on your workpiece.
This makes it suitable for any metalwork project, be it fabrication, car repair, or plumbing work. As for cutting depth, the Pilot Arc Plasma Cutter boasts an ideal clean cut of 12 mm and a maximum severance cut of 16 mm, allowing you to handle a broad array of workpieces with ease. In addition, this feature-rich tool adopts a unique air channel design to increase its heat dissipation efficiency, while its IGBT inverter boosts its performance to a further extent. In short, the VEVOR Pilot Arc Plasma Cutter is an engineering marvel known for its precision, cutting depth, and innovative features.
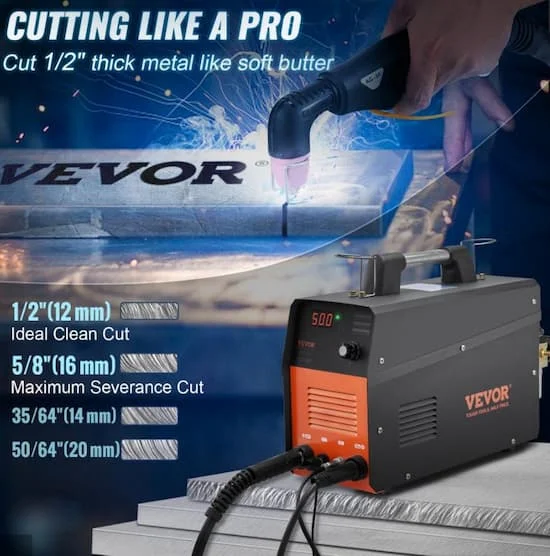
VEVOR Air Cutter with Plasma Torch
Also courtesy of VEVOR, the VEVOR Air Cutter with Plasma Torch is another powerful tool for metalwork professionals and hobbyists alike. In the first place, this plasma cutter boasts first-class cutting capacity, as attested by its 12 mm ideal clean cut and 16 mm maximum severance cut. With such a level of cutting prowess, hard metals will look like soft butter as you move the cutter along the cutting line.
Moreover, by integrating USB ports, you can connect USB fans, lights, and other devices to the VEVOR Air Cutter with Plasma Torch and enjoy the convenience they bring as you focus on your task. But equally praiseworthy is resilience against elements. By pressing on a single switch, you can activate its dustproof and waterproof features, and rest assured as you carry out your metalwork in wet or dusty environments. To wrap up, packing an abundance of features, the VEVOR Air Cutter with Plasma Torch effortlessly tackles any metalworking task in any scenario.
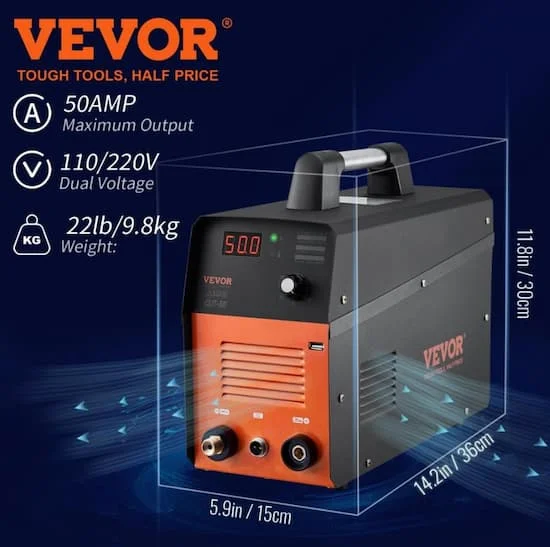
FAQ
What Can a Plasma Cutter Not Cut?
A plasma cutter, while adept at cutting a variety of materials, encounters limitations when faced with these two categories:
Non-Conductive Materials: Plasma cutters are unsuitable for non-conductive materials like wood and plastic, as these substances lack the electrical conductivity necessary for the plasma arc to function effectively.
Thick Materials: Plasma cutters may not be able to deal with exceptionally thick materials. As mentioned before, handheld plasma torches can only cut up to 38 mm, while automated plasma cutters fall short when facing metal plates thicker than 150 mm.
Can a Welder Be Used as a Plasma Cutter?
Generally no. Most welders cannot be used as plasma cutters due to limitations in intensity and precision:
Heat Intensity: Plasma cutters generate highly concentrated and intense heat through a plasma arc, essential for melting and cutting metals. Traditional welders, designed for joining metals, do not produce the same level of focused and high-temperature heat required for efficient cutting.
Precision and Cleanliness: Plasma cutters offer superior precision and produce cleaner cuts compared to welders. The concentrated plasma arc allows for intricate and detailed cuts with minimal distortion, a level of precision not achievable with most welding processes.
Can You Plasma Cut Rusted Metal?
Yes, plasma cutters can be used to cut rusted metal. Typically, rust does not hinder the cutting process much. However, rust does have the possibility of affecting the cutting quality, causing imperfections like uneven edges.
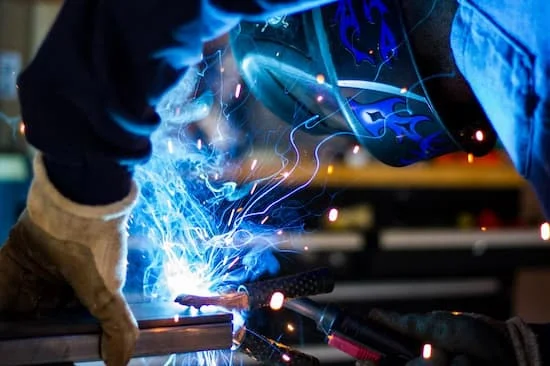
Conclusion
From our discussion above, the fact is now clear: how thick will a plasma cutter cut varies depending on factors like power source (or amperage), material type, consumables type and condition, gas selection, and so on. While general figures regarding the cutting capability can be put down, they by no means paint the full picture of plasma cutter max thickness. Ultimately, please consider all the factors affecting how thick can a plasma cutter cut and evaluate your practical needs to decide whether a plasma cutter is right for your project.