Have you ever wondered what the captivating world of aluminum plasma cutting looks like? You can picture this as precision slicing through aluminum, just like a hot knife slices through butter. Isn’t it smooth? That’s how plasma cutting works for aluminum. But why is it essential to know how to cut aluminum? It’s a secret skill that you must have in your toolkit. And if you master this art, you’ll find so many doors open for creating custom aluminum pieces that are sleek for a variety of projects.
This article will give you some top-notch advice regarding plasma cutting aluminum. And those straightforward insights will boost your game. You’ll also learn how to use the VEVOR plasma cutter. So, stick around to become a pro.
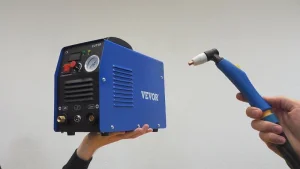
Can You Cut Aluminum with a Plasma Cutter?
Absolutely! Plasma cutting guarantees polished cuts and extreme precision for both steel and aluminum. Adjust the settings and amperage of plasma cutters to craft intricate lines and shapes on aluminum sheets. These versatile tools are not limited to metals; they can also be used on non-metals like plastics.
Cutting aluminum has become easy with the help of the VEVOR plasma cutter. Thickness is no longer an issue; you’ll get flawless and clean cuts with smooth edges. And above all, it’s a budget-friendly option.
There are some misconceptions as well about cutting aluminum with plasma cutter. One of them is that this method generates excessive heat. Plasma cutting does generate heat, but when done correctly, it produces smooth cuts and keeps the aluminum unharmed and cool. Another common myth suggests that it leaves rough edges behind. However, with proper technique, you can achieve smooth cuts. So, bust these myths and master the art of aluminum cutting.
How to Cut Aluminum with a Plasma Cutter & Tips for Precision?
Have you ever wondered how a plasma cutter cuts aluminum? What actions will keep the overall experience smooth and risk-free? Take a look at the guide below:
Step-by-Step Guide on How to Plasma Cut Aluminum
1. Safety First
Gear up before you start. Utilize all the required PPEs, including gloves, goggles, and appropriate clothing. Perform the activity in a well-ventilated area free from flammable materials. Additionally, have a fume extractor and a fire extinguisher nearby for added safety.
2. Components and Controls
Familiarize yourself with the components and controls of the plasma cutter:
- Current Display Meter: Shows the actual output current.
- Power Indicator Light: Illuminates when the power is on.
- Fault Light: Indicates overload or internal damage, requiring attention as per guidelines.
- Adjust the Value Knob: Clockwise to increase current, anti-clockwise to reduce.
- Cutting Gun Cable and Gas Connection Seat: Connect the cutting gun to the designated seat.
- Cutting Gun Control Socket: Two-core aviation socket to control the cutting gun.
- Negative Welding Terminal: Welding current flows through heavy-duty bayonet-type terminals.
3. Adjust the Settings
Prepare your VEVOR plasma cutter. Check its air pressure and adjust it according to your requirements. Select the appropriate nozzle and follow the procedure for cutting aluminum. Ensure the sheet you’re cutting is free from dirt and debris. Check for any exterior damage and ensure secure connections of components such as the cutting gun, cables, and ground clamp.
4. Power On and Operation
Start your plasma cutter for aluminum and adjust its speed based on the sheet’s thickness. Gradually increase the settings until you reach the desired set point. Continuously check the condition of the torch during this process.
Operation Steps:
- Turn on the power switch.
- Connect the welding holder and ground clamp.
- Connect compressed air to the cutting gun.
- Adjust air pressure using the regulator.
- Adjust cutting current as needed as shown below.
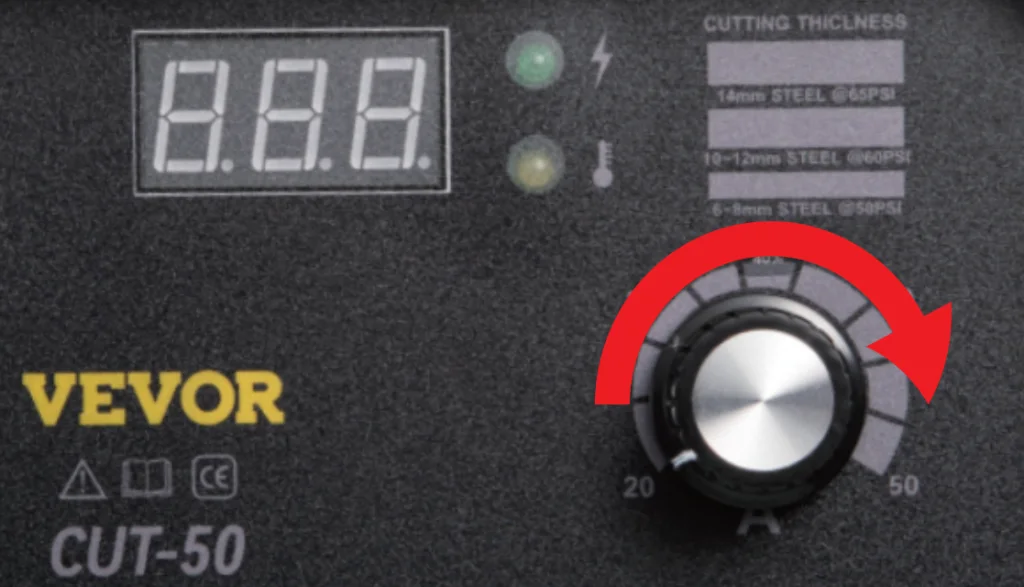
5. Execution and Cutting
Begin cutting by triggering the torch. Follow proper techniques for hand torch cutting. Practice piercing when necessary. When cutting aluminum, keep the torch perpendicular to the sheet’s surface, touch the metal with the torch tip to ignite it, and guide the arc along the cutting line. The plasma cutter will efficiently cut aluminum within some time.
Ensure you execute each step properly to achieve safe plasma cutting of aluminum.
6. Post-Cut Inspection
After completing the cutting process, inspect the edges for accuracy and smoothness. Use specific tools such as a wire brush to remove debris. Ensure a thorough post-cut inspection to maintain the quality of your work.
Tips for Precision
When we talk about precision while using a plasma cutter for aluminum, there are some techniques we need to master. Take a look at some of the tips for precision while plasma-cutting aluminum:
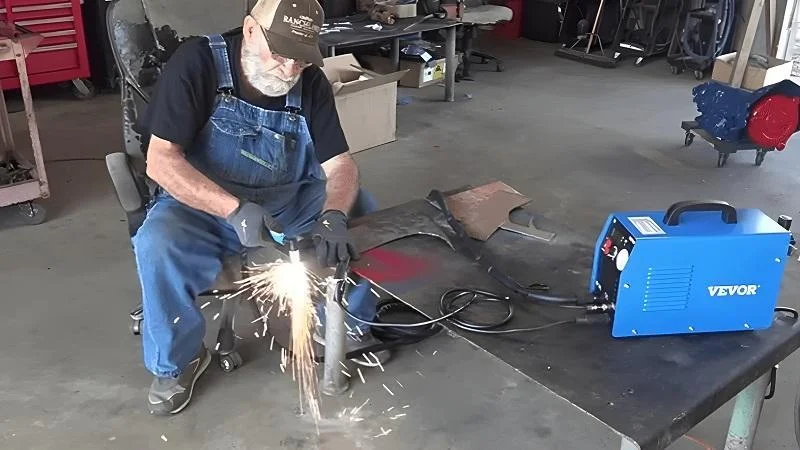
1. Optimal Speed and Angle
If you’ve got an idea of how to cut aluminum, you must know how to balance speed and angle. For that, you must maintain a steady pace while moving the plasma cutter torch. Also, maintain a consistent angle relative to the sheet’s surface. This may take some time, but keep experimenting with angles and speed till you achieve your target.
2. Consumable Maintenance
Keep inspecting the consumables such as nozzle, shield, and electrode from time to time. Ensure that they’re free of debris to get smooth cuts.
3. Choosing the Right Plasma Cutter
When selecting the plasma cutter for aluminum cutting, it’s important to consider specialized options tailored for this purpose. VEVOR offers a range of high-quality plasma cutters that cater to aluminum cutting needs. Among them, the VEVOR 50Amp Non-Touch Pilot Arc Plasma Cutter stands out for its pilot arc technology, ensuring stable and consistent cutting. The built-in air compressor of the CUT-40Z 40 Amp Air Plasma Cutter enhances portability and efficiency, making it a reliable choice for aluminum projects. Additionally, the VEVOR Plasma Cutter, 50 Amp, Non-Touch Pilot Arc Air Cutting Machine is designed for ease of use and efficiency, featuring a heat emission hole for steady performance. When exploring VEVOR’s plasma cutter options, carefully assess each product’s features to ensure they align with the specific requirements of aluminum cutting, ultimately ensuring optimal efficiency and precision.
4. Effective Torch Height Control
To obtain precision, it is crucial to maintain torch tip height and position. For correct height, you may use height control systems that automatically adjust the distance from the sheet’s surface
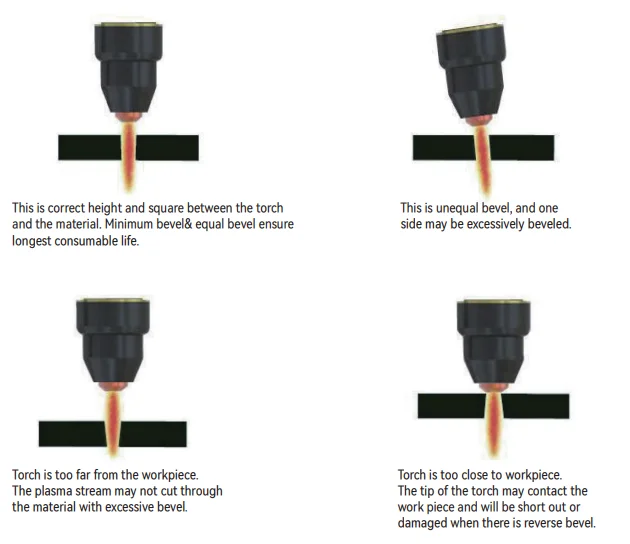
.
Check out the video; it will help you achieve clean and straight cuts using plasma cutting:
5. Power Source Settings of VEVOR Plasma Cutter for Aluminum
Understanding the power source settings is important to ensure the fine cutting of aluminum. Fine-tuning all these will ensure smooth and precise cuts. Keep a welding extension cord as well to ensure a constant power supply. The current needs to be adjusted under the metal thickness to achieve the best cutting experience.
Thickness | Current | ||
Inch | MM | Ampere: below 240V | Ampere: below 120V |
10 Gauge | 3 | 15A-50A | 15A-35A |
1/4 | 6 | 25A-50A | 30A-35A |
3/10 | 8 | 35A-50A | 35A-50A |
3/8 | 10 | 45A-50A | – |
1/2 | 12 | 50A | – |
6. Utilizing CNC Technology
In order to obtain unmatched precision, opt for integrating CNC technology into the cutting process. The programmed designs ensure automated cutting with precision as well.
So, based on all the tips mentioned above, you can get an idea of how to cut aluminum with a plasma cutter with accuracy.
Safety Measures for Plasma Cutting Aluminum
When using a VEVOR plasma cutter for cutting aluminum sheet, it’s crucial to implement comprehensive safety measures:
- Safety Gear:
Equip yourself with gloves, goggles, and a welding helmet. Consider these items as essential protective equipment, not just accessories.
- Proper Ventilation:
Ensure the workspace has adequate ventilation to eliminate metal dust and fumes generated during the cutting of aluminum plates.
- Flammable-Free Zone:
Maintain a workspace free of flammable materials and have a fire extinguisher nearby for immediate response to unforeseen incidents.
- Avoid Touching Output Terminals:
Do not touch the output terminals while the machine is in operation to prevent electric shock.
- Handling Aluminum Scraps:
Exercise caution when handling aluminum scraps after cutting, as they may retain heat. Use a blanket or fire pit mat to manage them safely and dispose of scraps responsibly at recycling centers.
- Cool Down Period:
Allow the plasma cutter to cool down before storing it to ensure optimal functionality and safety.
- Thermal Overload Protection:
If the machine is overused, used in high-temperature environments, or poorly ventilated areas, the thermal overload switch may activate, stopping the machine. Keep the power on, and the built-in fan will work to lower the temperature. The machine will be ready for use again when the internal temperature reaches a safe level.
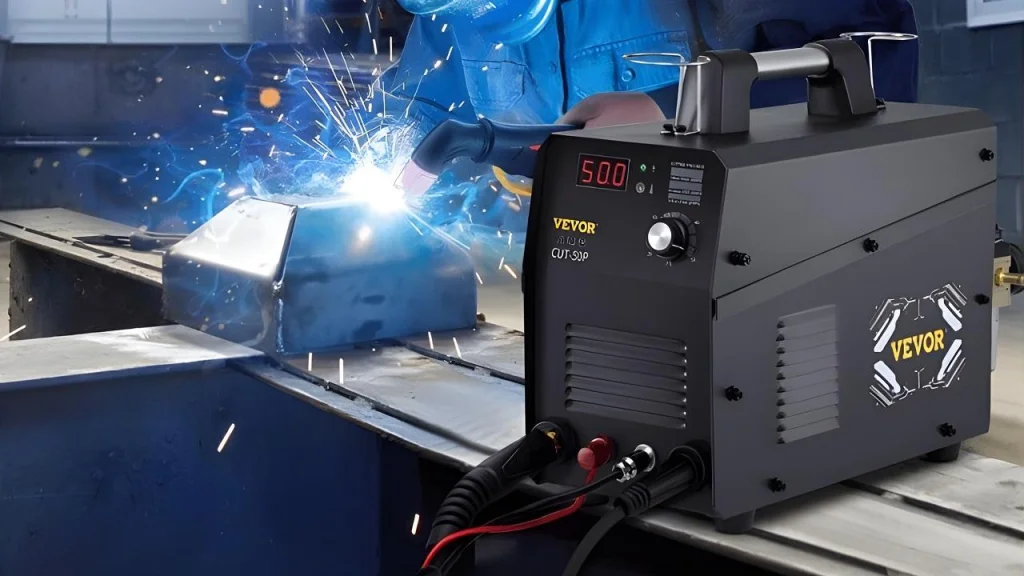
FAQs
What Makes Plasma Cutting a Good Choice for Aluminum?
Plasma cutting is an ideal choice for aluminum because of its swift nature as well as precision. It doesn’t matter whether the plate is thick or thin, plasma cutting delivers clean edges.
Can Plasma Cutting Be Used for Complex Shapes in Aluminum?
Yes, plasma cutting is good at handling complex shapes. It is a versatile method that delivers detailed cuts and designs, making it easy for users to create diverse shapes. Navigating through complex patterns on aluminum sheets is not easy, unless you are using plasma cutters. That’s what makes them an obvious choice for all kinds of industrial applications.
Are There Any Special Considerations When Plasma Cutting Aluminum?
There are a few special considerations when plasma cutting aluminum. One of them is gas selection, which is important to prevent oxidation and produce clean cuts. Besides that, adjustment of amperage and power settings is crucial. Inspect the consumables regularly and maintain a constant angle and speed to avoid any mistakes. And don’t forget to take proper safety measures to ensure a healthy environment.
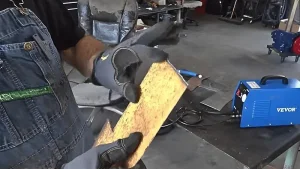
Conclusion
Plasma cutting is unarguably the best cutting method for all kinds of metals, non-metals and even plastics. But to obtain precision, you must have the right tool, adjust its settings and consider safety measures. Use these tips to enjoy a seamless cutting experience for your aluminum projects. And to make it even better, try VEVOR plasma cutter. It’s time to elevate your game, make as many designs as you can and turn your ideas into reality.